With the continuous investment of high-power grid connected wind turbines from various countries around the world and the vigorous development of aerospace industry, the demand for silicon nitride ceramic bearing balls is strong in both domestic and international markets.
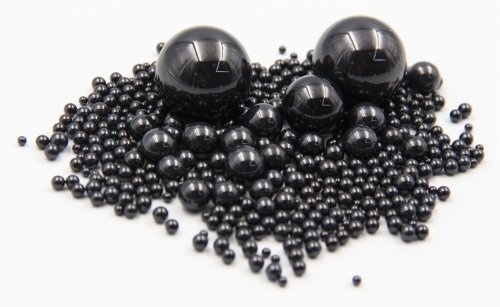
The reason why it can be applied in the above fields is because silicon nitride ceramic materials have high hardness, wear resistance, low density and thermal expansion coefficient, excellent high temperature resistance, non magnetism, corrosion resistance, high thermal conductivity, self-lubrication, and excellent thermal shock resistance, oxidation resistance, and many other characteristics. Therefore, it is the preferred material for bearing balls working in high temperature, high-speed, high-precision, and special environments.
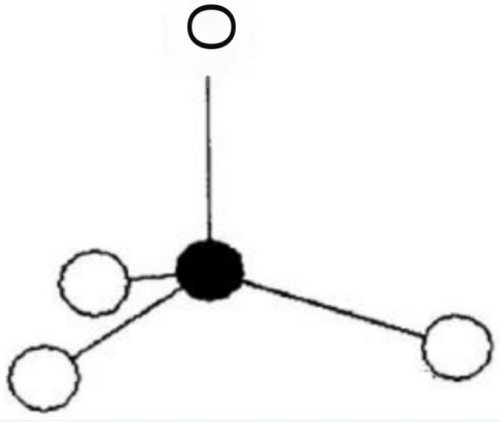
Note: Si3N4 is an inorganic substance with high hardness, lubricity, and wear resistance. The Si-N4 tetrahedral structural unit is formed by covalent bonding of 1 Si atom and 4 N atoms, and the tetrahedral unit forms a three-dimensional spatial network. The special structure makes the hardness of silicon nitride material very high, with a Mohs hardness of about 9. Therefore, the material performance of silicon nitride material can remain stable at high temperatures of 1400 ℃.
1. The Spheroidization Principle of Silicon Nitride Ceramics
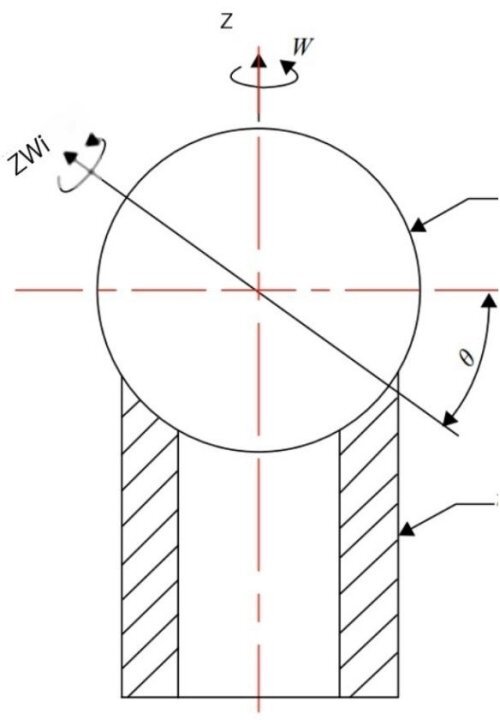
At present, there are roughly two types of mechanical grinding and polishing methods for ceramic balls: one is the cup shaped grinding tool processing method, which is characterized by the ability to continuously change the rotation angle of the ball and high processing accuracy. However, only one ball can be processed at a time, and is often used to produce high-precision balls in standard balls and positioning systems. Another type is the grinding disc processing method, which is currently the main method for producing ceramic balls. It can process thousands of balls at once, with high efficiency but low accuracy. In addition to mechanical polishing, new technologies for ultra precision machining of ceramic balls such as magnetic fluid polishing, chemical mechanical polishing, and ultrasonic assisted polishing have also emerged in recent years. By adopting these new “flexible” machining techniques, micro cutting of ceramic ball surface materials can be achieved, allowing for the removal of allowances through plastic fracture, thus obtaining a super smooth and undamaged surface.
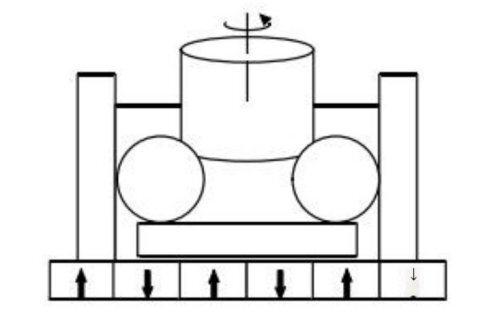
However, regardless of the grinding and polishing method, the basic principle is to achieve efficient material removal through abrasive particles and grinding fluid. Under the action of abrasive particles and grinding fluid, the processing deterioration layer of the sphere gradually decreases or is removed, resulting in a smooth or ultra smooth sphere. As a hard brittle material, ceramic balls have high requirements for various components in the grinding fluid due to their low surface energy The main components and functions of grinding fluid
Silicon nitride ceramic balls belong to hard brittle materials, and their processing techniques mainly include mechanical grinding processing technology, chemical grinding processing technology, and chemical mechanical grinding processing technology. These grinding methods all require grinding fluid to assist in processing, which can remove materials and also provide surface finishing treatment for the workpiece.
The selection of grinding fluid has a significant impact on the efficiency and accuracy of grinding processing, and its role is different in the coarse and fine grinding stages. The coarse grinding stage focuses on improving grinding efficiency, while the fine grinding stage improves grinding accuracy. Grinding fluid is mainly composed of abrasive particles, grinding base fluid, and additives. During the grinding process of ball billets, abrasive particles act as cutting tools and can remove surface allowances. The hardness and size of abrasive particles affect processing efficiency and accuracy; The base liquid is the carrier of abrasive particles and needs to meet the requirements of sufficient suspension of abrasive particles; Additives are mainly used to assist in abrasive grinding and improve the grinding environment. The main functions of each component in the grinding fluid are as follows.
01). The role played by abrasives
(1) Grinding action
Radial cracks are subjected to a force directed towards the interior of the workpiece, which can develop towards the interior and damage the workpiece, reducing the original hardness of silicon nitride materials. However, this phenomenon does not develop rapidly. As a brittle material, silicon nitride ceramic balls can also be removed through plastic removal under certain processing conditions. The critical condition for brittle removal can be calculated through the indentation fracture mechanics model. When this condition is lower than the critical condition for brittle removal, the material removal of silicon nitride ceramic balls is mainly plastic removal, and the critical condition is related to the compressive load and the hardness of the abrasive particles. Therefore, When the pressure load is determined, the abrasive particles in the grinding fluid will have a certain impact on the grinding effect of silicon nitride ceramic balls, so the selection of abrasive particles in the grinding fluid is very important.
In addition, chemical reactions may occur during the grinding process, which can change the properties of the surface material of silicon nitride ceramic balls, converting the harder silicon nitride material into silicon dioxide material, thereby reducing the hardness of the ball surface, achieving better material removal effect, and improving the surface quality of the processed parts.
In terms of abrasive selection, if you want to have the best effect on the workpiece, you must choose abrasive particles that have high hardness, high strength, good toughness, high stability, chemical stability, and self sharpening properties when selecting abrasive particles. Generally speaking, the hardness of abrasive particles must not be lower than the hardness of the workpiece being processed, otherwise it is impossible to effectively grind the workpiece. However, it should not be too high, as high hardness often leads to wear of the grinding tool and shortens its lifespan.
For the grinding process of high hardness silicon nitride ceramics, carbide abrasive particles and diamond like abrasive particles are generally selected. Silicon carbide has the characteristics of high hardness, high strength, good chemical stability, and good thermal stability, making it the most commonly used material in ceramics. Silicon carbide can maintain its chemical properties under high temperature, high pressure, strong acid, and strong alkali conditions, and has a relatively small friction coefficient, so its wear resistance is relatively good. Diamond has the characteristics of high hardness, high melting point, and low friction coefficient, which are also suitable for grinding silicon nitride ceramics. However, diamond is expensive, and considering economic issues, diamond abrasive particles can be used for ultra precision grinding.
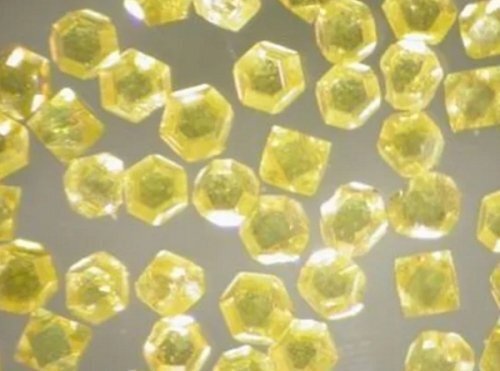
2. Role played by liquid phase medium
(1) Lubrication effect
After the surface material of silicon nitride ceramic balls is removed, the debris is dispersed in the solution, which has a significant impact on the surface quality of the ball. However, the lubrication effect of the grinding fluid can form a lubricating film between the ball and the debris, improving the rotation or rolling efficiency of the ball. The surface of the ball is protected, which helps to improve the efficiency of grinding processing and can improve the material removal rate while avoiding damage. The base fluid in the grinding fluid is the main lubricating medium, and boundary lubrication is achieved through the action of water. When in contact with the surface of the workpiece, adsorption and reaction films are formed, which can effectively protect the workpiece and improve its rotation ability.
There are two main types of adsorption membranes, namely physical adsorption membranes and chemical adsorption membranes. The physical adsorption film is mainly formed by the van der Waals force between particles in the grinding fluid, which attracts each other and exists in low load and low speed grinding environments; The chemical adsorption film is mainly formed by the chemical reaction between polar molecules in the grinding fluid, and exists in high temperature, high load, and high speed grinding environments, which can effectively protect the surface of the workpiece.
(2) Cooling effect
The cooling effect of grinding fluid refers to the ability of the grinding fluid to absorb the heat generated by the mutual compression between the ball and abrasive particles during the processing, reducing the temperature of the ball surface and avoiding problems such as surface damage caused by excessive temperature. The grinding fluid flows through the processing area, taking away processing heat through the fluidity of the fluid and liquid vaporization, reducing the temperature of the processing area and protecting the processed parts. The temperature of abrasive particles in the processing area will also increase. In order to ensure the self sharpening performance of abrasive particles and enhance grinding efficiency, it is necessary for the grinding fluid to have good cooling performance.
The cooling performance of the grinding fluid is influenced by the thermal parameter values and flowability, and the thermal parameter values in the grinding fluid are determined by the specific heat capacity and thermal conductivity rate; The fluidity of a liquid is mainly determined by its permeability, which depends on the surface tension and viscosity. When the surface tension is high, the grinding fluid on the surface of the ball will become a droplet like liquid. At this time, the contact angle between the solution and the surface of the ceramic ball is large, which weakens the permeability of the grinding fluid and reduces its cooling ability; When the surface tension is low, the grinding fluid on the surface of the ball will be evenly dispersed. At this time, the contact angle between the solution and the surface of the ceramic ball is small, and the permeability of the grinding fluid is enhanced, making its cooling ability stronger.
(3) Suspension effect
There is a certain interaction between abrasive particles, which can affect the form of abrasive particles in the grinding fluid. There are mainly two different forms: one is agglomeration form, and the other is dispersion form. There are three main types of interactions between abrasive particles, namely electrostatic interactions, van der Waals interactions, and steric hindrance interactions.
The dispersion effect of abrasive particles in the grinding fluid is mainly determined by the base liquid. When the base liquid medium shows hydrophilicity, hydrophobic substances will have a certain repulsive effect on water, leading to agglomeration and precipitation. Therefore, hydrophilicization treatment should be carried out on it. When dispersing abrasive particles in the grinding fluid, it is necessary to make a judgment on the physical properties of the abrasive particles. The size and hydrophobicity of the abrasive particles will have a certain impact on the dispersion effect of the grinding fluid. There are many dispersion processes for abrasive particles in the grinding fluid, including mechanical stirring, ball milling dispersion, and ultrasonic dispersion. Among them, ultrasonic dispersion has a better effect, and the distribution of abrasive particles in the grinding fluid is relatively uniform, resulting in higher stability of the grinding fluid.
(4) Cleaning effect
The chips generated during the processing of silicon nitride ceramic balls are not cleaned in a timely manner, and the chips stay between the workpiece and abrasive particles for a long time, or adhere to the surface of the workpiece. This not only scratches the surface of the ball, but also affects the processing efficiency. By adding some surfactants to the grinding fluid to enhance its cleaning ability, these additives can reduce the adhesion ability of debris and prevent it from being carried away by the flowing grinding fluid, thus avoiding damage to the surface of the workpiece. The cleaning ability of grinding fluid is related to the fluidity and pressure supply of the liquid. When the fluidity of the grinding fluid is strong, the cleaning ability will also be enhanced. For example, the cleaning effect of grinding ceramic balls with water medium is greater than that of grinding with oil medium.
3. Summary
The dimensional accuracy and surface quality of ceramic balls have a significant impact on the lifespan of bearings, and in order to pursue dimensional accuracy and surface quality, it is necessary to pay attention to the selection of grinding fluid. By analyzing the main components and functions of the grinding fluid, a more targeted design of the polishing fluid formula can be achieved, which will be of great significance for the development of efficient and low-cost ceramic ball grinding polishing fluids.