-
1 +
Years
Industry experience in China
-
1 +
Highly skilled employees
-
1
sq. ft.
Manufacturing factory
who we are

Other benefits include:
▪Variable wall thicknesses
▪Tighter tolerances
▪Fewer steps from raw material to finished part
▪Fast production cycle times
▪Reduction in material scrap
▪Long tool life, especially for zinc and magnesium

▪High strength and hardness
▪High thermal conductivity
▪High electrical conductivity
▪Outstanding EMI/RFI shielding properties
▪Good finishing characteristics
Separately, each die cast alloy offers a variety of benefits that the other may not offer. That is one of the great things about die casting, you do not have to be limited when it comes to choosing the right metal.
Die Cast Process
There isn’t one single process that can suit every project. Each project is different which is why Innovacasts offers multiple solutions for all die casting needs. This ensures the right process is always used for the right application. At Innovacasts, we offer three different types of die casting processes.
Hot-Chamber
Used for zinc, some magnesium alloys, and other low-melting, hot-chamber die casting is a great option for alloys that do not readily attack and erode metal pots, cylinders, and plungers.

Cold-Chamber
Better suited for metals with high melting points such as aluminum, during cold-chamber die casting, metal is liquefied and then ladled into a cold chamber where a hydraulically operated plunger pushes the metal into the die.
Injected Metal Assembly
Over the past 12 years, we have developed and refined our innovative; one-step manufacturing solution, Injected Metal Assembly. IMA outperforms most adhesives used for small component joining and assembly production and reduces manufacturing costs.
Every day we work collaboratively to find new opportunities and discover unique, high-value solutions for your product manufacturing.
-
Ready To Get Started?
From prototype to production, our team of engineers is ready to help bring your idea to life.
- GET AN INSTANT QUOTE
How We Can Help
-
Upload your design
Just simply upload your CAD files and submit RFQs with clear information online.
-
Design analysis
We'll send you design for manufacturability analysis and transparent pricing.
-
Start production
Our experts will produce your parts with the required technologies and materials.
-
Receive your parts
Once parts pass quality inspections they are well packed for delivery.
-
Integrated Approach, Customized For You Get Your Product To Market
- Get A Custom Quote Now
WHY Choose Innovacasts
-
Excellent Quality
Certified Factory
ISO-9001:2015
Customer Satisfaction
95+/100
Quality is everything for us. It's why we've developed the advanced tools and techniques to deliver the results you need with the cost effectiveness your business demands. We've pioneered innovations that are now the foundation for an entire industry. Innovations such as:
•Thin wall aluminum die casting enabling you to build smaller and lighter products at lower component costs
•Eliminating costly machining so you benefit from shorter lead times and improved yields
•A unique, high-speed, multi-slide technology to deliver you net shape the first time
And that's just the start
Today, we deliver over 1 million precision components globally every year. And every one of our 9 facilities facilities worldwide is dedicated to a program of continual improvement.
read more -
ON-TIME DELIVERY
Prototype Model Making
3-9 Days
Rapid Injection Molding
2-5 Weeks
We know unreliable delivery impacts your bottom line - from expedited freight premiums to potential loss of customers to maintaining higher than normal safety stock levels.
Which is why we do things differently:
With 9 plants in 3 countries, we're physically closer to where you need us—lowering freight costs and accelerating response times
We can engineer in one location and simultaneously launch in multiple global geographies
We can span production across multiple facilities to offer you unprecedented scale and massive volumes
Just-in-time manufacturing which delivers higher productivity and faster time to market
High-speed, multi-slide equipment allows for quick changeovers delivering greater scheduling flexibility
And because we know our equipment inside out, our delivery commitment to you is always based on knowledge rather than estimate
It means you're assured consistent, on-time delivery, more satisfied customers, and better business.
See how our commitment to on-time delivery could improve your business, talk to us about your next project.read more -
Friendly Service
Customers Served
800+
Fast Response within
12 Hours
With one-on-one support service from a professional technical sales team that responds quickly within hours and always attends to every detail of your needs, you will have a great customer experience from start to finish.
read more
-
Driving The Future Forward
Business active in
30+ Countries
Lower than US/EU prices
30%+
In everything we do, we always consider how we can do it better. Innovation is the yardstick we work by as we create the advanced tools and techniques to move the industry forward.
This delivers some important benefits:
•We can help you take your products further while shortening lead times and lowering costs
•We've invented new multi-slide technologies that are redefining the results you can expect every day
•These technologies eliminate secondary operations such as machining, increasing manufacturing speeds and offering you reliable results with no capacity constraints
•Innovations such as thin wall aluminum die casting deliver higher strength components at a fraction of the weight
•And injected metal assembly (IMA), also known as insert molding, outperforms most adhesives for small component joining and assembly—all while reducing manufacturing costsUltimately, our innovation is about your business, delivering you higher quality components and a better product, every single time.
See how our innovative techniques could improve your business, talk to us about your next project.
read more -
Great Experience
Projects Delivered
300+ Per Month
Parts Manufactured
20,000+ Per Month
Comprehensive production capacity, including in-house machining and post-processing, and integration of manufacturing resources across China. This allows us to fully meet your needs for any project from prototype to production.
read more
Client
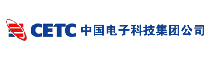
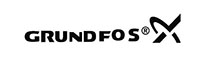
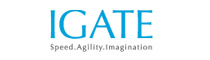
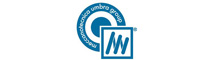
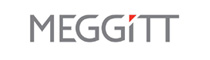
Great Teamwork, Motivated Staff, Consistently Delivering Excellent Work For Our Customers.